Text by Will Quam, Photographs by Will Quam & Conrad Szajna for Bricks Incorporated | Download PDF
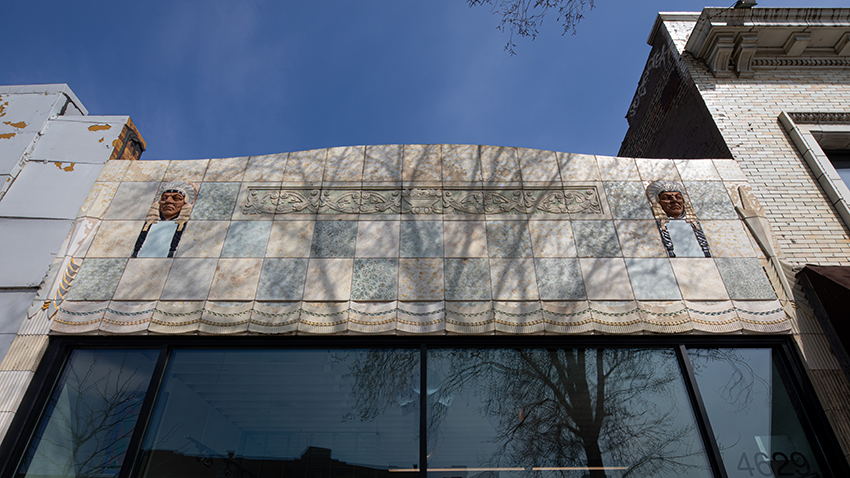
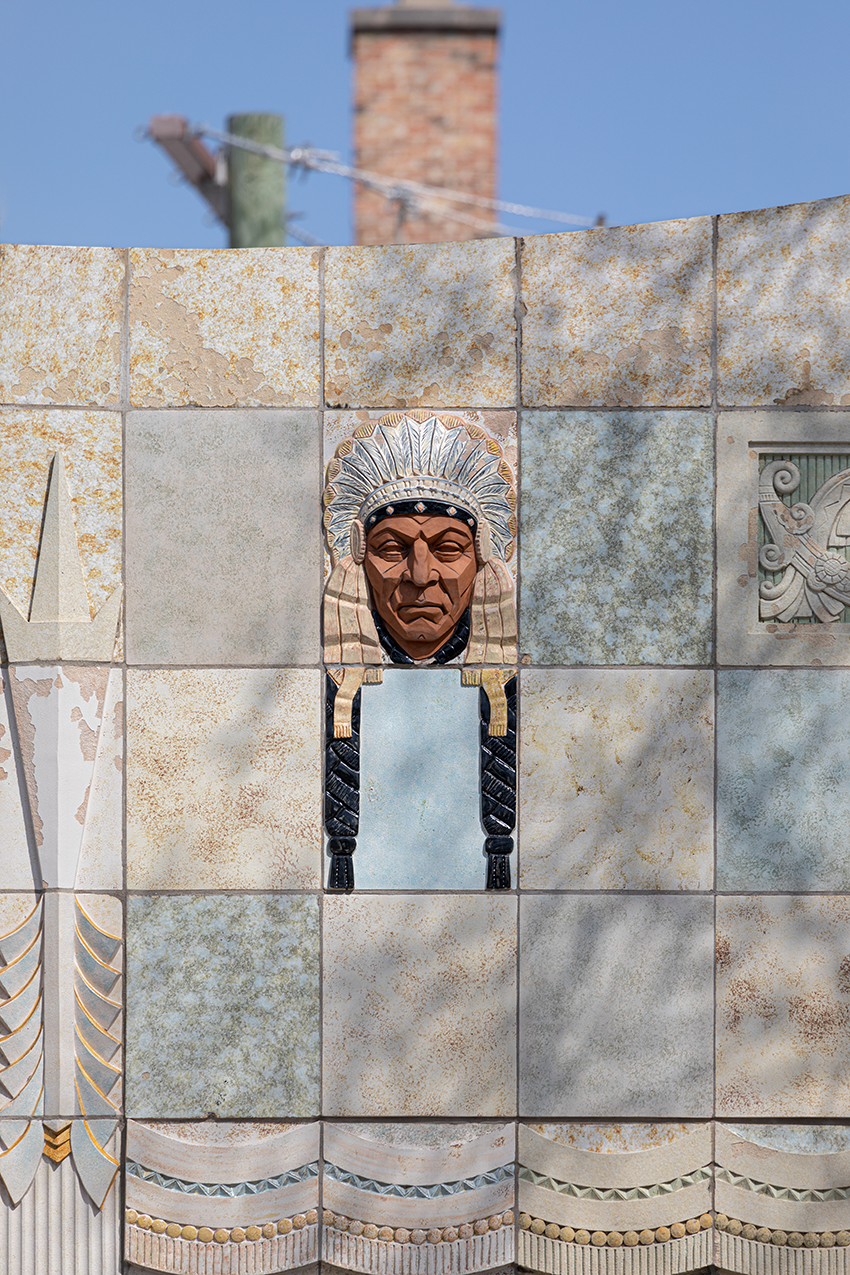
4629 N Broadway
When a one of a kind historic terra cotta building fell into slow disrepair, it seemed almost a matter certainty that nothing could be done.
Fortunately, thanks to new ownership, old-world craftsmanship was able to breathe new life into this deteriorated building.
The Building
Built in 1930, 4629 N Broadway was constructed in the thriving Uptown neighborhood of Chicago. At the time, this neighborhood was the 20’ss hub for movies, music, and the excess. All along Broadway, the excitement and wealth of that era can still be seen along the architecture through it’s liberal use of terra cotta. Stunning terra cotta was displayed on banks, movie palaces, towers apartment buildings and everything in between.
Terra cotta, created by sculpting clay into decorative blocks that could then be copied and glazed in many different colors, truly made ornate facades possible for any kind of building–even a shoe store, the original use of 4629 Broadway.
Designed by architect Carl Hauber, 4629 Broadway is a slim one story building with large display windows framed by flued terra cotta pilasters and blocks with blue and gold garlands. Above the window the mottled terra cotta alternates blocks of blue and white in a checkered pattern with an inset panel of flowers and classical imagery.
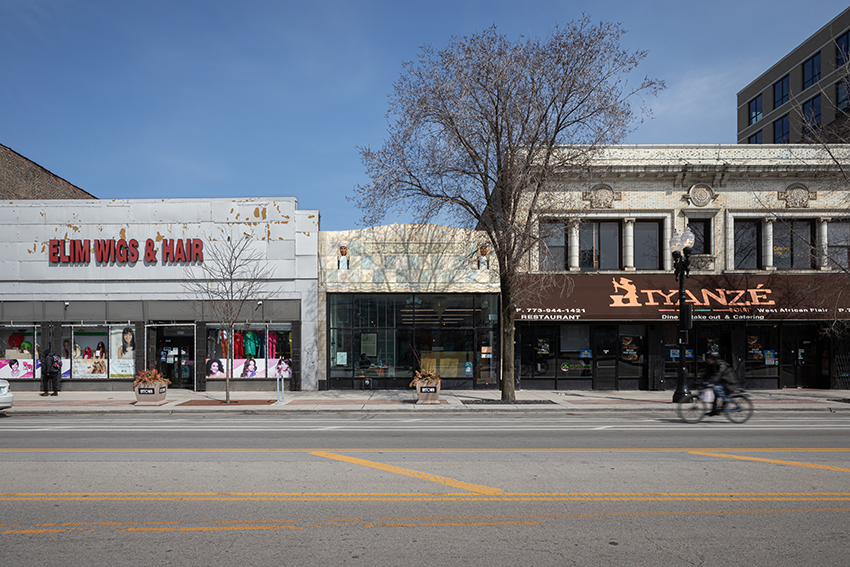
The most striking and unique parts of the terra cotta facade are the two stern and sharply angled men depicted as Native Americans with their headdresses that flank either side of the facade.
AThe faces have an Art Deco quality in their abstraction that is balanced by a delicate realism in the silvery-blue flowers of the headdress.
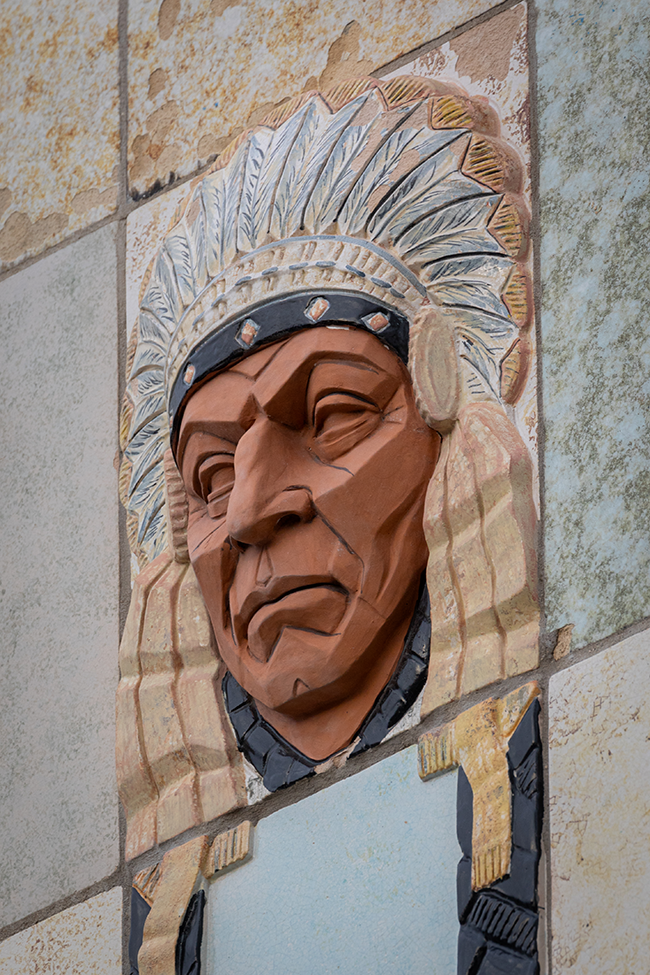
The Damage
By the early 2000’s, 4629 Broadway, had lived many lives and seen many different tenants. Each tenant’s needs had been different, causing the facade to be altered or changed little by little over the decades. Paint had been slathered on in layers, signs had been affixed and removed, bolts and hardware had been driven through the terra cotta blocks and in some areas, plywood had even replaced several of the original pieces.
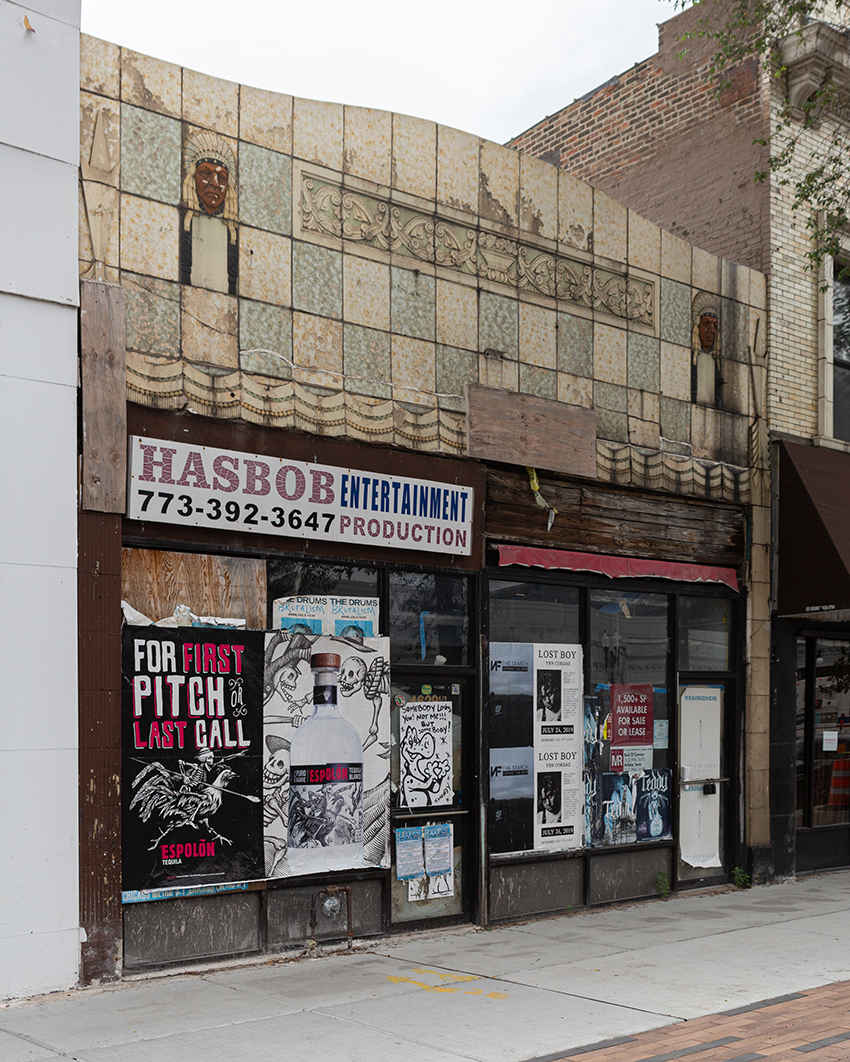
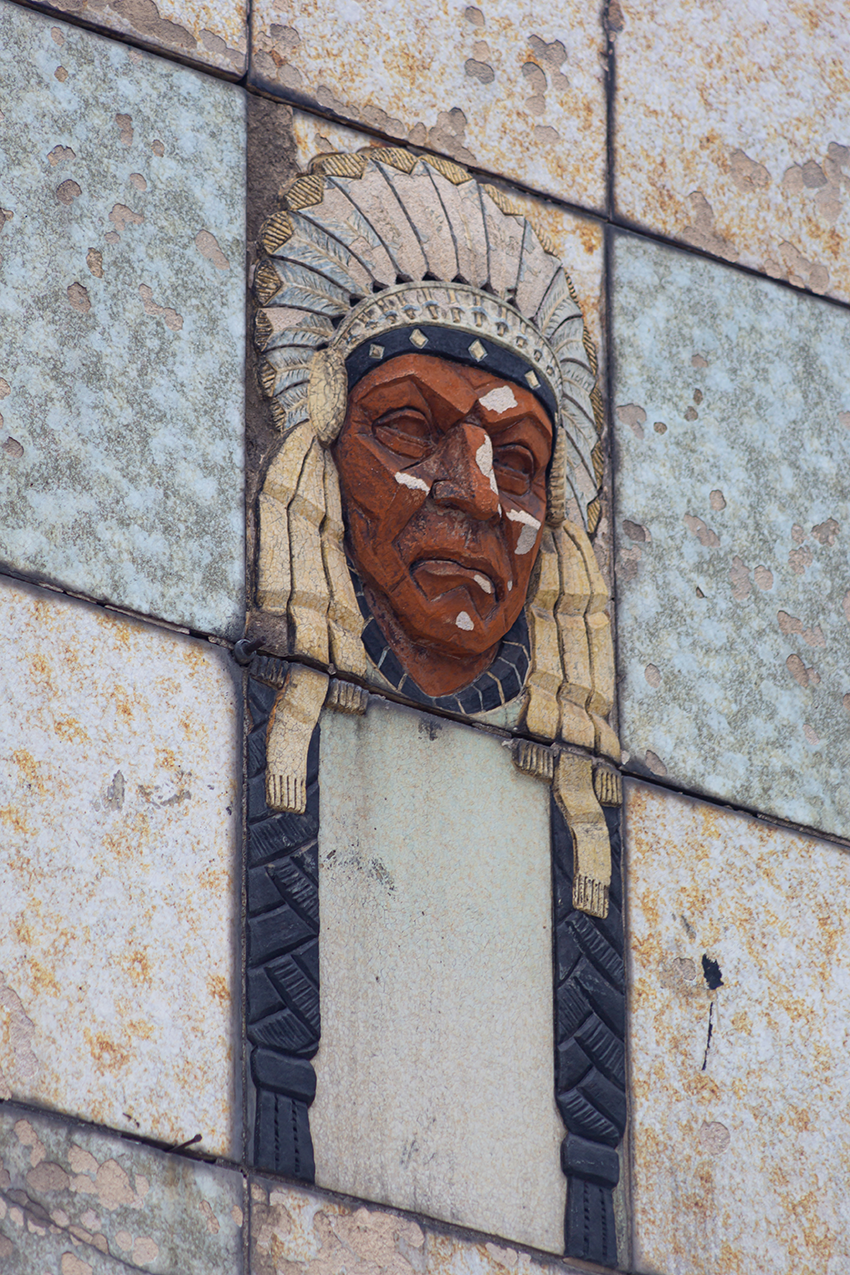
Unfortunately, the faces had not fared any better than the blocks. They were left chipped and broken; hardly recognizable from their state during installation nearly 100 years earlier. The face shown on the right was covered in so much soot and dirt, that all the angular demarcations had nearly been lost. On the left, the face had lost large pieces of the cheek, chin, nose and forehead. On both, feathers on the headdresses had were mostly lost.
Overall, the terra cotta facade was in dire condition.
Thankfully, a new owner stepped in with a passion to return the building to it’s original state.
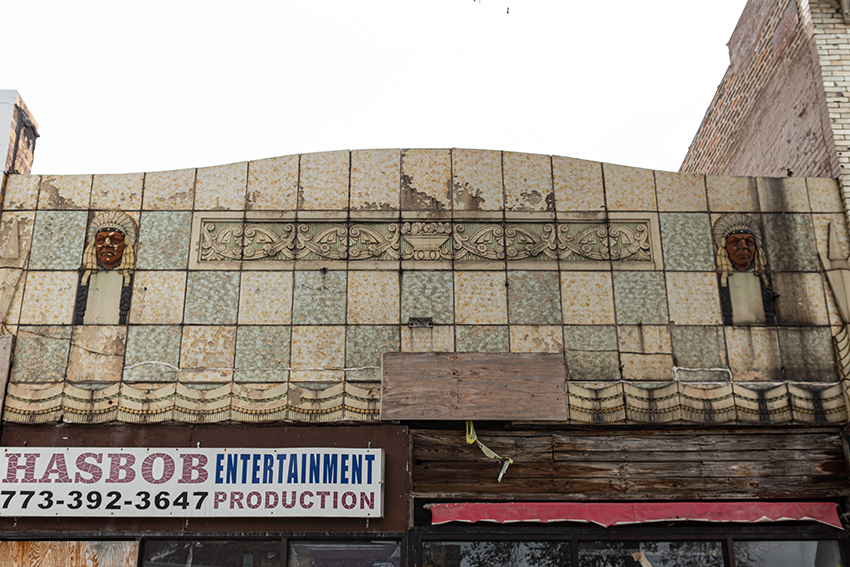
To begin the restoration and reparation process, the first step was to assess the the condition the facade was in.
“It was in dire shape,” says Conrad Szajna of Formed Space, the general contractor on the project. “Numerous pieces were cracked and crumbling. We had to pay special attention and take our time removing each individual layer”.
It was determined that a full facade restoration would be too complicated and costly, thus it was decided to attempt to maintain as much of the existing materials as possible and only recreate what was necessary.
In order to remove the facade, Formed Space worked slowly and carefully from the top down, row by row and block by block. Just prior to the removal of each piece, it was photographed, tagged and marked on a map of the facade. This detailed inventory process of each piece would facilitate putting it back together again.
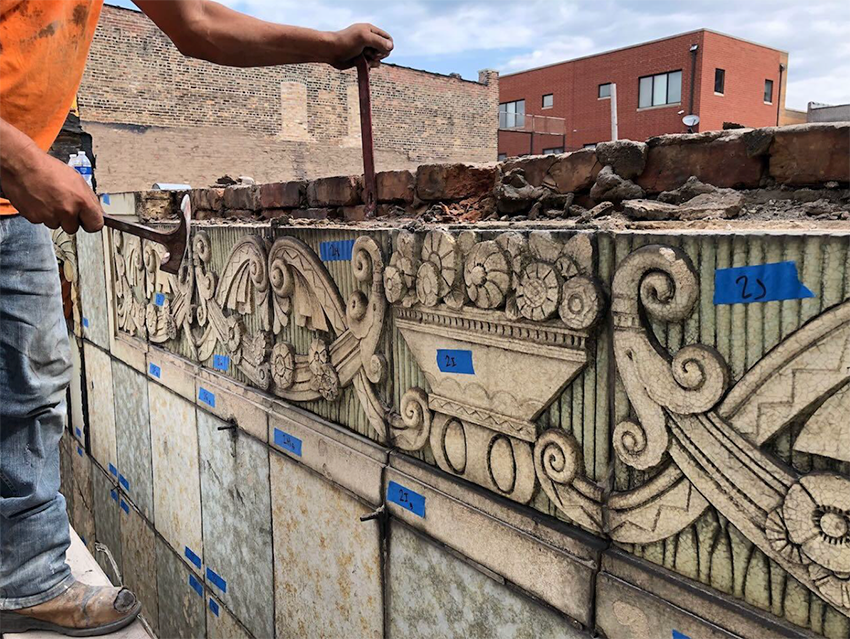
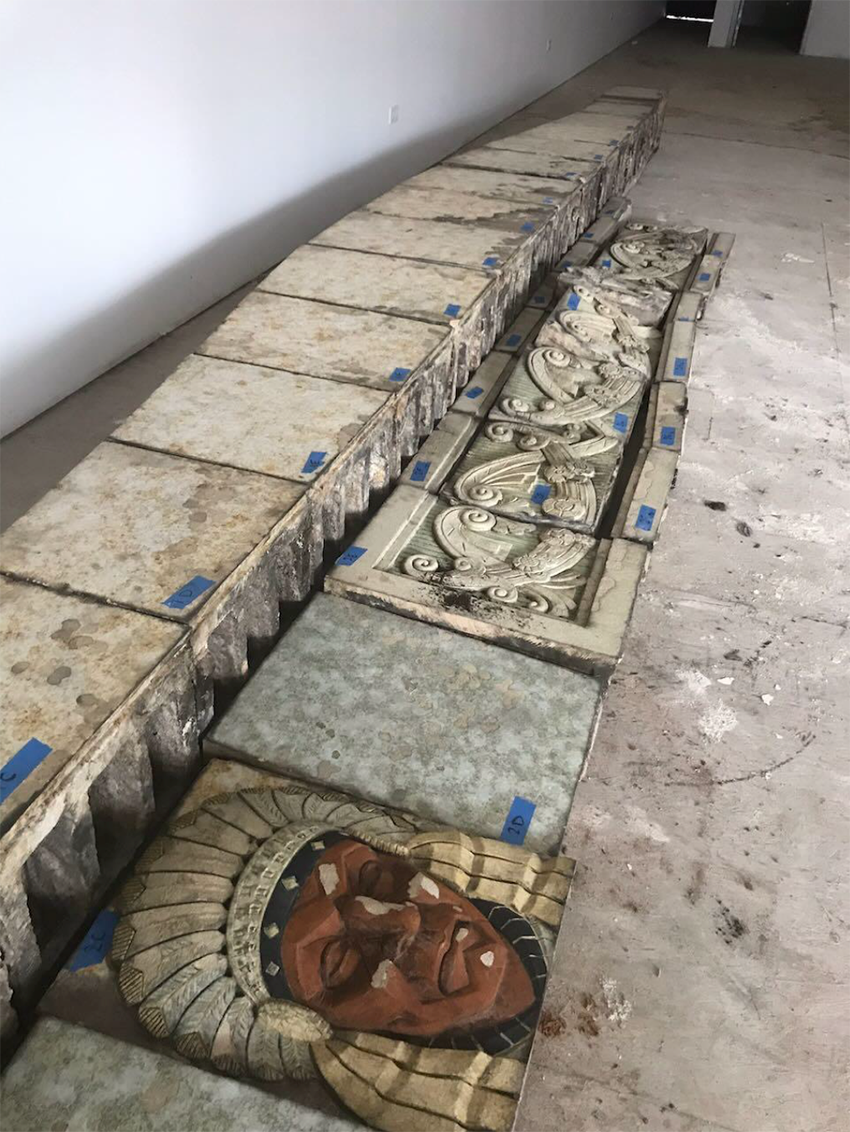
As each piece came off, they were kept onsite. The facade was reassembled, this time the floor, inside the building. This allowed the team to clearly see the pieces up close and inspect every side of them. Finally, a full picture of the facade’s overall condition could be thoroughly visualized.
At this point in the restoration process, Mr. Szajna decided it was vital to collaborate with Bricks Inc. Together they would decide what pieces would be salvageable . “They are my go to when it comes to any sort of brick work and historical work,”says Szajna, “I’ve worked with Bricks Inc for 10 years or so and we’ve done some crazy projects with brick and terra cotta. They’re just so knowledgeable and willing to help out”.
Based on the conditions f the pieces, it was determined that approximately 1/3 of the terra cotta was still in good condition. Another 1/3 needed minor repairs and the final 1/3 needed to be completely recreated. With that said, the facade was packed up and shipped to Brick’s Inc. Little Village yard for the next steps.
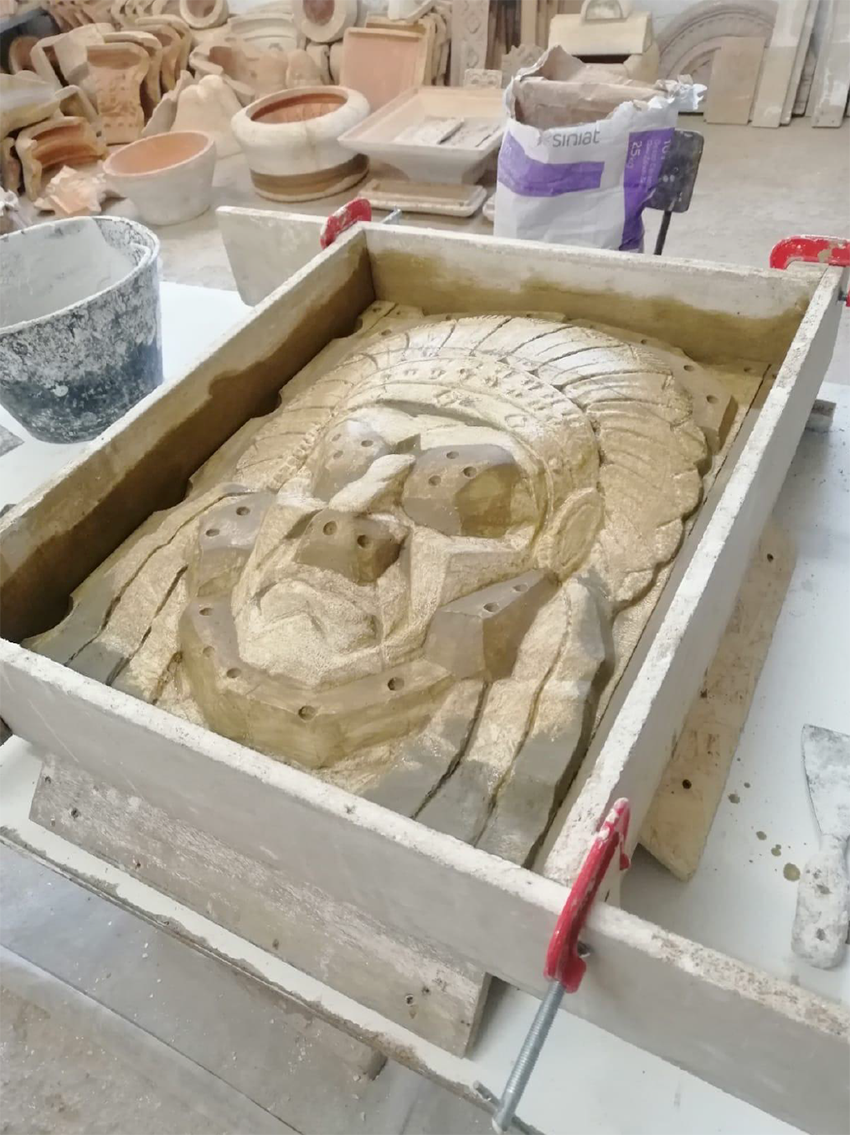
Remaking
Repairing terra cotta is not substantially difficult. Recreating it is a completely different story.
How does one rebuild decorations that were made nearly 100 years ago? The unfortunate reality is that the company that made the original 4629 Broadway terra cottas and their molds, have been closed for more than half a century.
Thankfully, for the team, the facade was symmetrical . While some pieces were missing or damaged beyond recognition, there were others that survived enough to be heavily analyzed and used as templates to recreate additional matching pieces. Once the “template” pieces were removed and cleaned, they were packaged and shipped to the terra cotta fabricator in the ancestral homeland of architectural terra cotta: Italy.
For decades, Bricks Inc. has had a close working relationship with San Anselmo. Similar to Bricks Inc., San Anselmo is a family owned company. Just outside of Venice, Italy, San Anselmo’s family has been hand making bricks for over four generations. They are not just manufacturers but rather artists, sculptors and chemists, experts in clay and glaze.
Some of the most challenging pieces to recreate for this project, were of course the angular faces with the very ornate headdresses. Not surprising, these are not the first terra cotta faces San Anselmo has had to create or even re-create in clay. In the past they have even been able to recreate terra cotta faces based solely on photographs. With the original heads in hand, this project was comparatively a walk in the park for these sculptors. They used the originals to make intensely detailed measurements of every feature and angle and eventually were able to make new molds.
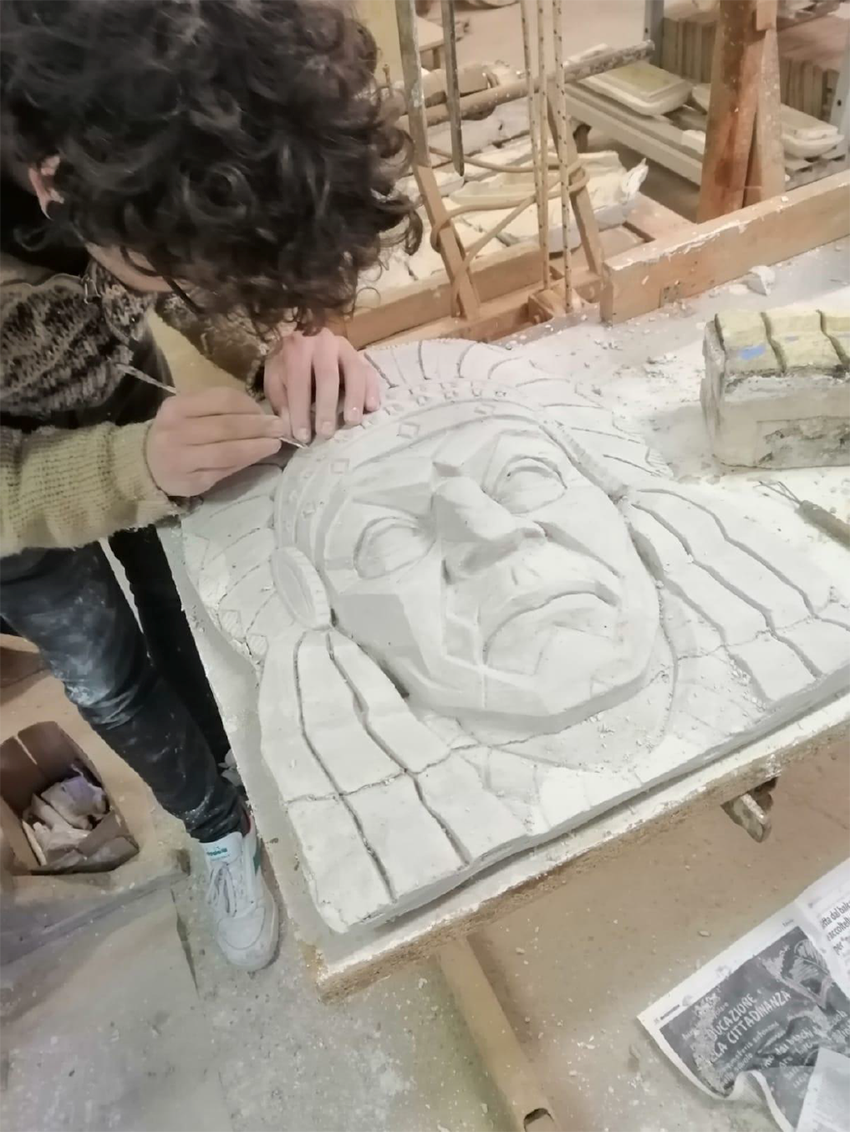
The most difficult part of the entire process was not the sculpting, but the glazing of the terra cotta. The originals were not a single solid color but rather mottled mixtures. “There are multiple colors on many of those pieces,” says Dave Kafer of Bricks Inc., “with a base color and then top colors sprinkled and applied on top.”
What it really came down to was San Angelo attempting techniques over and over and over again in order to see what process would come closest to those 100 year old terra cotta pieces.
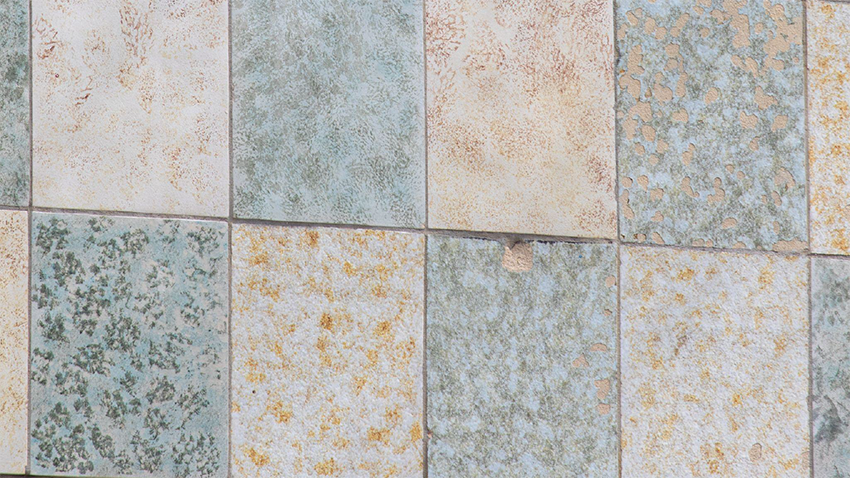
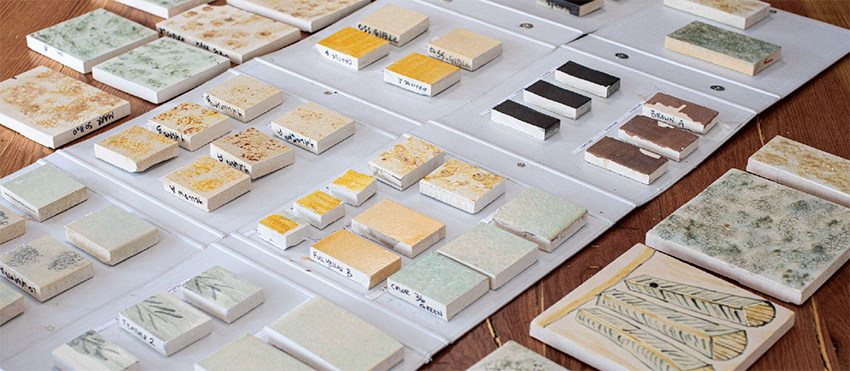
They tried applying the layers of glaze with brushes, with towels, with rollers, by spraying. “And you don’t really know what you’re going to get because the glaze is a totally different weapon when its fired,” says Kafer.
Throughout the test process, San Anselmo was continually updating the Chicago team with pictures, video calls and even physical samples shipped across the Atlantic. “We really counted on Bricks Inc. to guide the team,” said Szajna. The number of stakeholders had grown and included the landmarks Commission, who had to give approval on the final glaze. Thankfully, “Bricks Inc. did a great job of communicating between us and the manufacturer out in Italy”.
All of this back and forth can add up. That’s where working with an experienced manufacturer such as San Anselmo is so important. “They only had to try about 15 different pieces and techniques before they got it,” says Kafer, “we know we can really rely on their artisanship”.
The successful technique? Soft sponges dabbed across the surface, but you would never know it. It looks just right, next to the originals. With final approval of the sculpted blocks and glazes, from all the stakeholders, the new terra cotta was now on its way to Chicago.
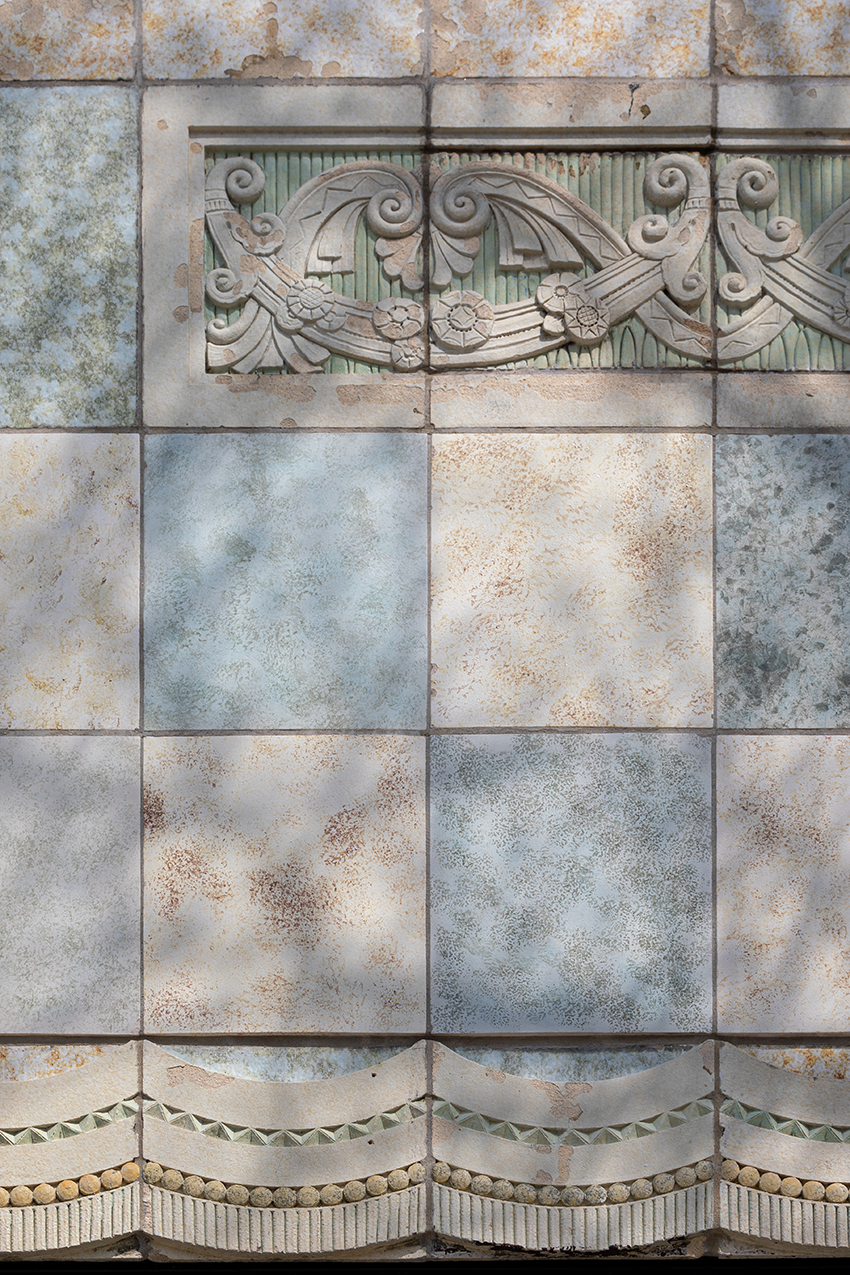
Upon arrival, the new terra cotta was blended with the old pieces that were previously salvaged. Szajna and Formed Space were now responsible for returning it to its rightful place in Uptown. At the time the facade was to be installed, the building was being occupied and it could not be brought inside the building for storage. Instead it was safely stored at Bricks Inc, in their warehouse in Little Village. Every day, Bricks Inc. delivered between 8 and 10 terra cotta pieces; this was as many as could be installed in a day.
At 4629 Broadway, Formed Space received and reassembled the terra cotta pieces. This time around, they worked from the bottom up. The facade was also treated and installed with new moisture barriers techniques and rust proof stainless steel ties in an attempt to preserve them as long as possible.


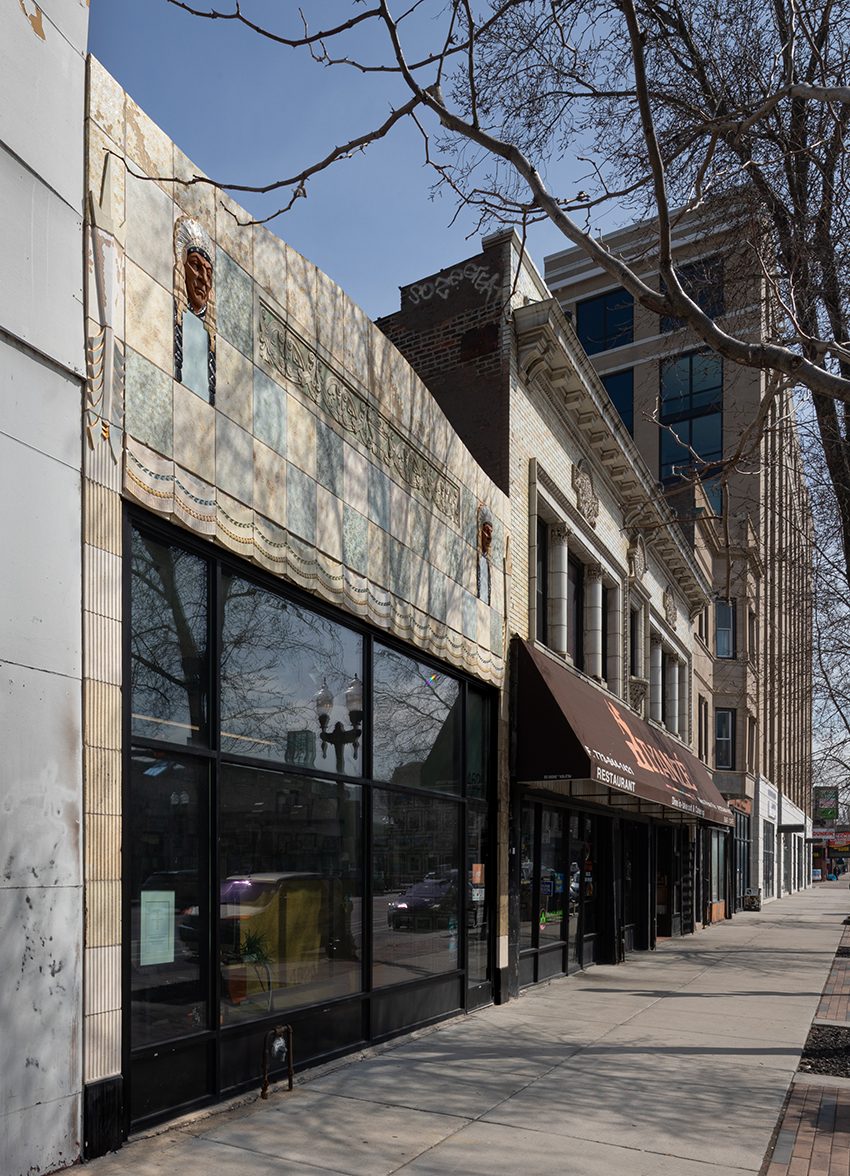
Conclusion
This kind of work does not happen every day, especially not on a small building like this. Many would have just replaced the entire thing and thrown the gorgeous, yet cracked terra cotta, into the dumpster. Not here; thanks to dedicated ownership, skilled tradespeople and trusted relationships with artistic partners, some parts of history remained salvaged.
“It took a lot of coordination,” says Szajna, “and it’s kind of crazy how a small facade like that evolved into a large team across the seas, it was a fun thing to do”.
“Had we not involved Bricks Inc., I think it would have been much more challenging,” he adds. “But we got them involved super early so they really guided and told us what to look out for. There’s a lot to know about these historical buildings and it can be hard to understand how they’re put together, but we were able to anticipate it after working with them (Bricks Inc.)”.
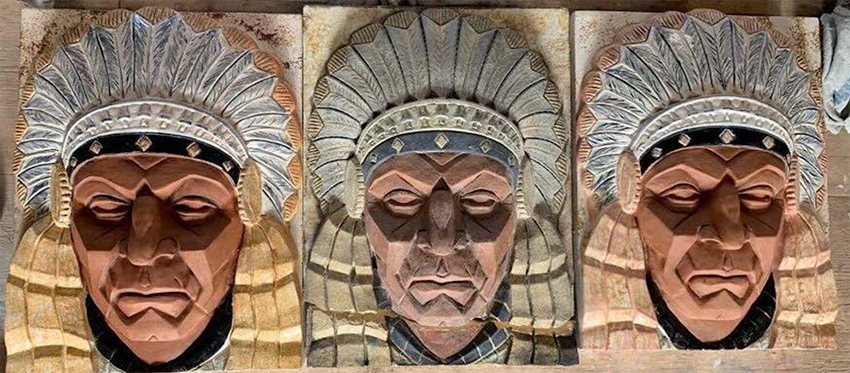
4629 N Broadway
Client: Tag Capital LLC
Architect: MDT Architects
Contractor: Formed Space
Terra Cotta: San Anselmo, custom work
Case Studies in Brick
Text by Will Quam
Photographs by Will Quam & Conrad Szajna
www.brickofchicago.com