Text and photographs by Will Quam for Bricks Incorporated | Download PDF
Before Kathy Bentley and Mark Hoffmeister had a house, they had a brick.
On a walk through Lincoln Park, Bentley spotted a brick wall and fell in love. When Bentley and Hoffmeister contracted architect Robert Sellars to build a new house, she gave him the address and sent him to look. “It was this great… dark brown, purplish brick,” says Sellars. “It’s really stunning.”
How often does the brick supercede the house? Not often. But in this case, it did, and it led Robert Sellars and Bricks Inc.’s Brent Schmitt on a unique and rewarding journey.
Selecting The Brick
“Usually the brick selection process comes much later,” says Sellars. But for the house at 1853 N Burling Ave, the first thing Sellars and Bentley needed to do was visit Brent Schmitt at Chicago Bricks Inc.
“I was involved very early on, because the homeowner came in and said ‘this is what I’m looking for,’” Schmitt says. Schmitt then worked with Bentley to identify the characteristics of her wall that she wanted to emulate in her home. Identifying a tumbled and vintage look, Schmitt then showed Bentley samples that fit the look she was going for: machine molded brick, extruded brick put under rollers, waterstruck brick, and so on.
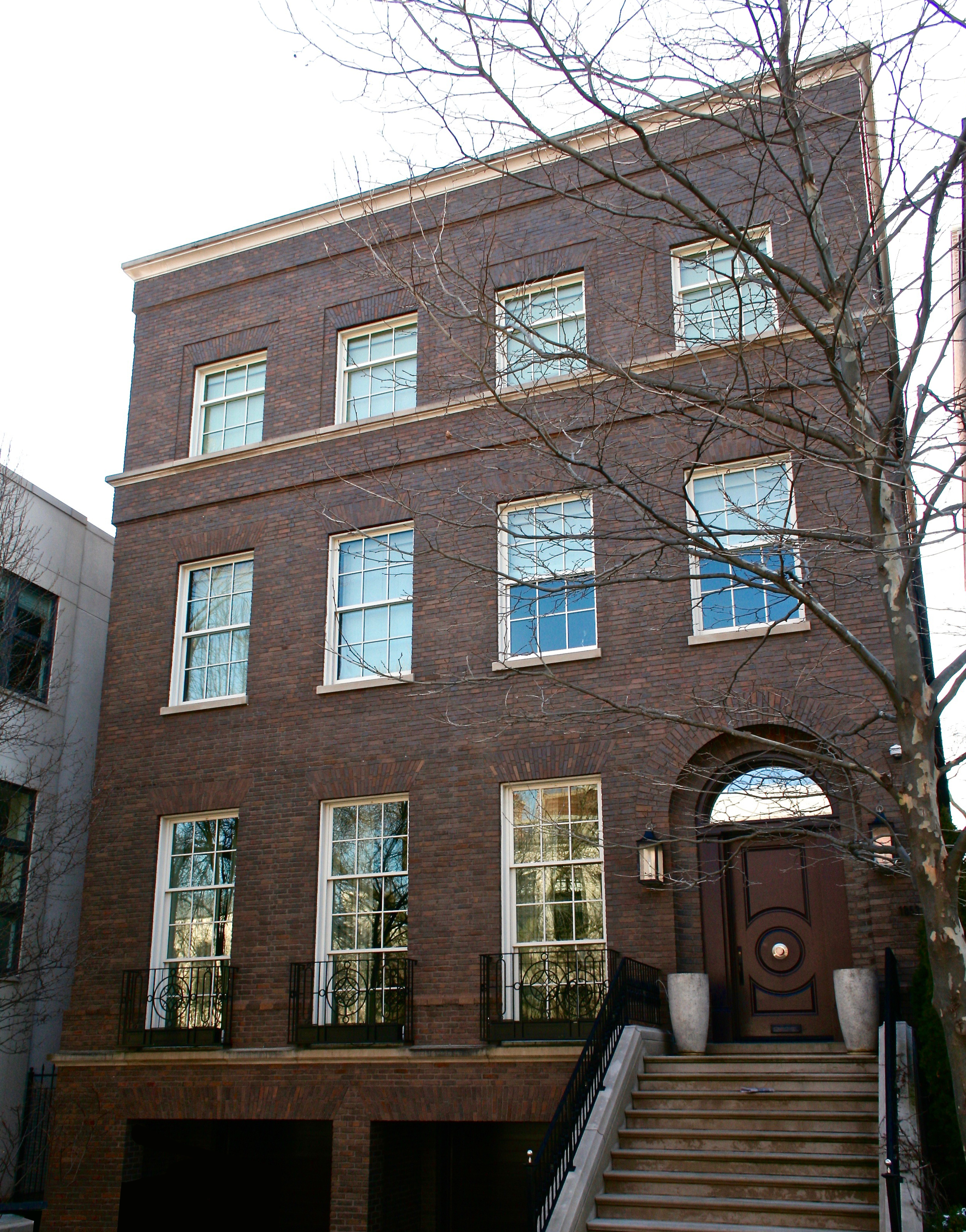
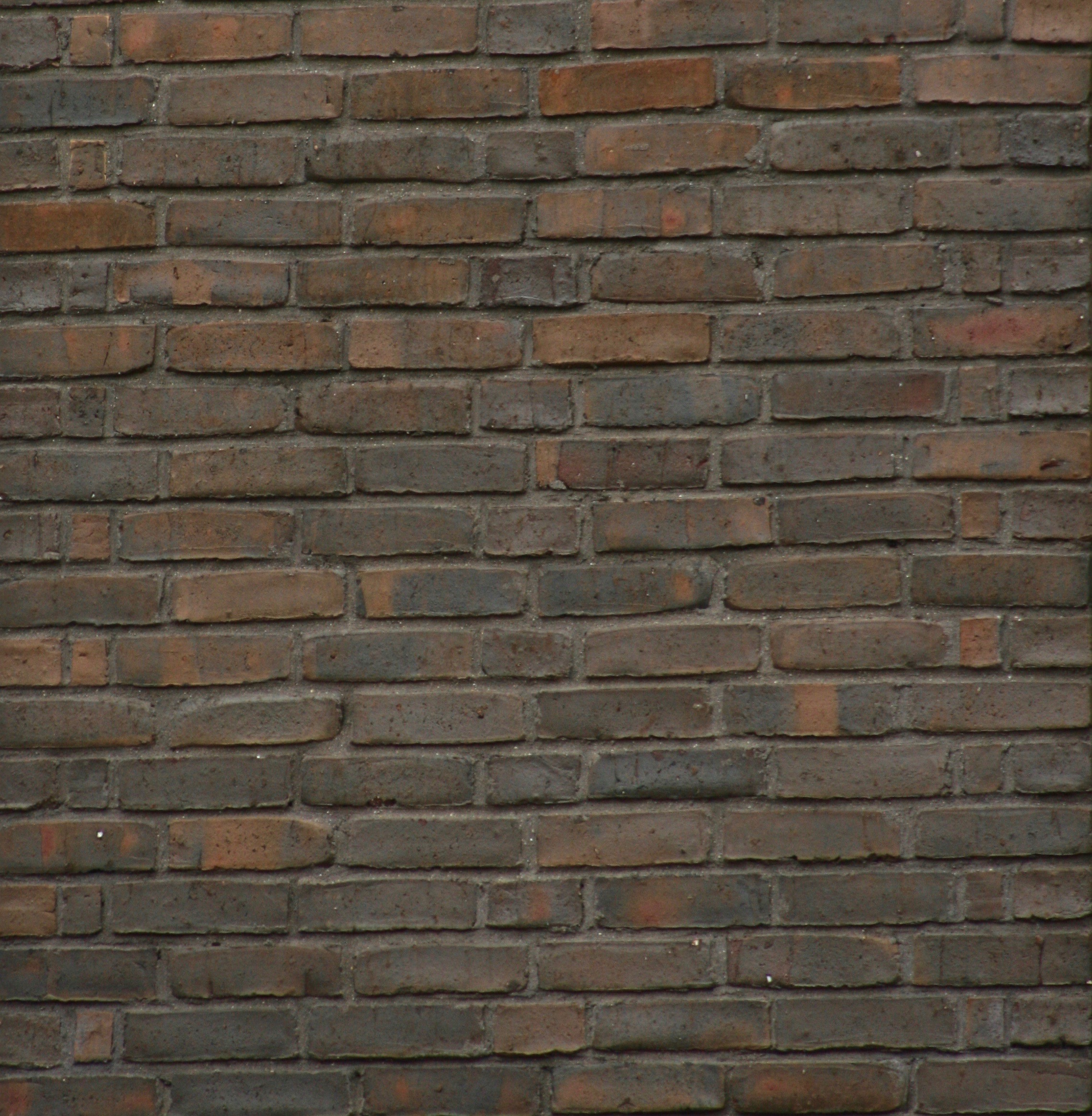
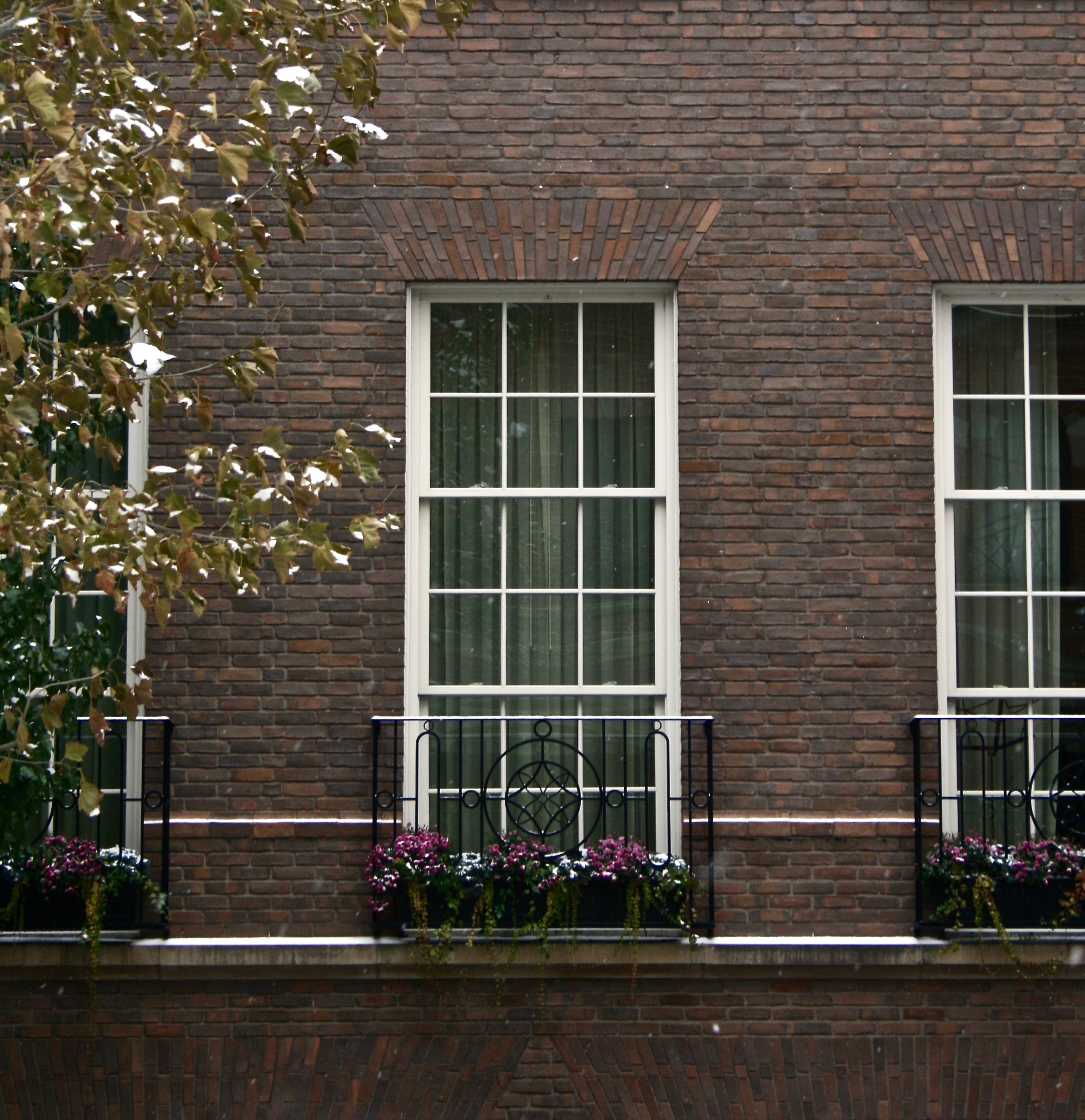
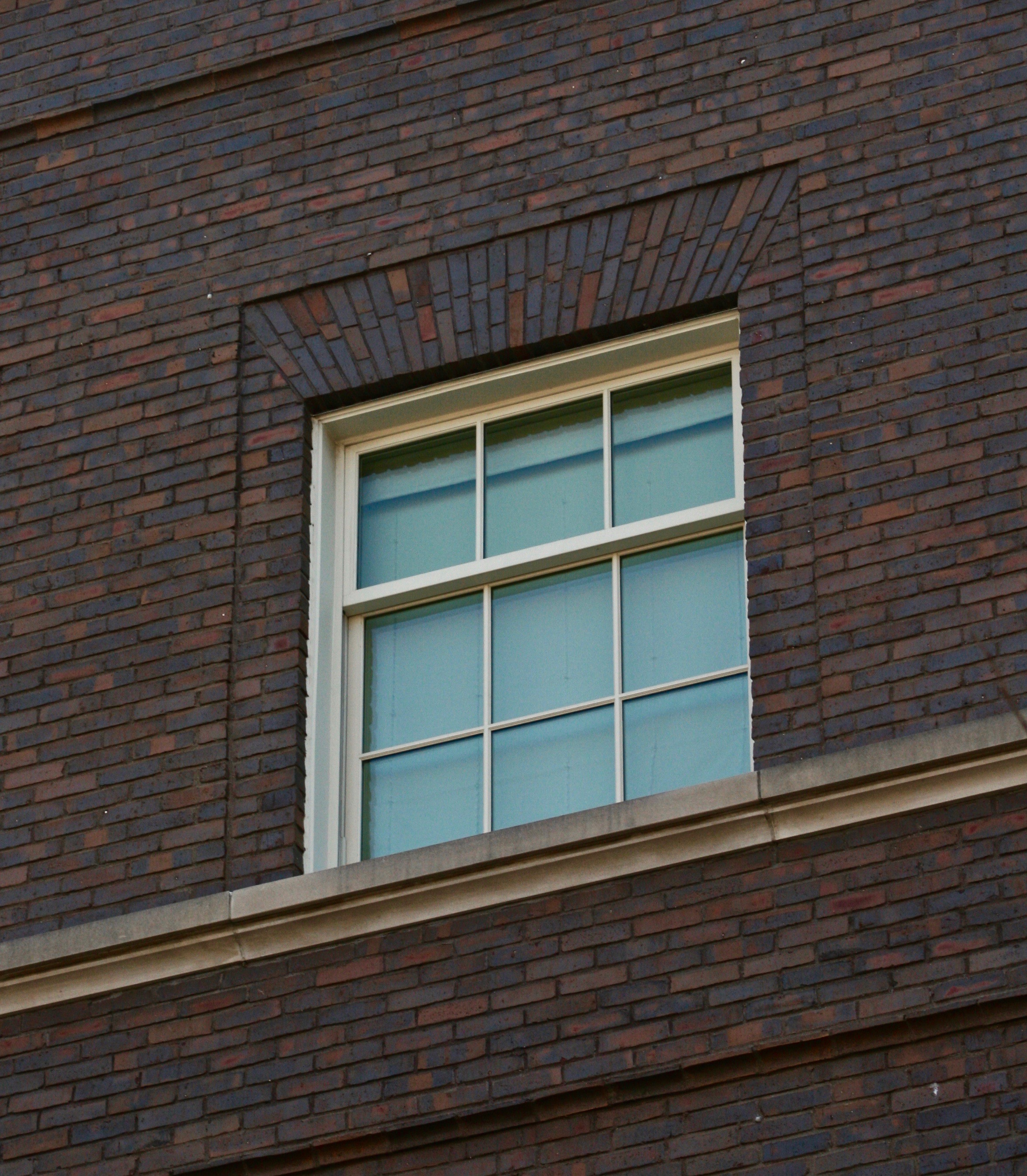
It was waterstruck “Bennington B&B” brick by Vermont Brick ended up taking the cake when it came to replicating the look that Bentley desired.
Waterstruck brick is made by forcing clay into molds lined with a liquid solution – the “butter in the baking tin,” which allows the brick to release from the mold after packing. Each brick is packed into and slid out of its own individual mold, rather than cut from the same massive block of clay. This means that the patina and shape of each brick slightly differs from that of its neighbors, giving the brick the quality that homeowner Kathy Bentley sought.
This uniqueness is especially clear when comparing the waterstruck bricks used on 1853 N Burling Ave. with a similar extruded product.
Sellars’ design also required special and uniquely shaped bricks. Special wooden molds were made, one for each shape. For Schmitt, the most impressive part of the process was Vermont Brick’s attention to detail. “Every single brick gets touched,” says Schmitt. And that makes a difference.
In the firing process, a percentage of the bricks naturally developed red “hearts” — spots where a brick burned hotter due to it position in the kiln. Bentley and Hoffmeister felt that these red bricks didn’t suit their vision, so Schmitt had the red bricks culled from the final mix.
“He was really, really helpful in honing everything,” says Sellars.
With Vermont Brick’s Bennington B&B selected and perfected, the time came to build the house around it. For both Schmitt and Sellars, one thing was always clear. “The brick was meant to be the star of the show.”
Designing With Brick
The 1800 block of N Burling Avenue is dotted with older red brick buildings, new luxury homes clad in limestone, and a 1937 yellow brick Chicago Public School. The couple wanted a fairly traditional house that both fit in and stood out from the block. For Sellars, the street itself presented a unique challenge toward the design of the house. “Everything is pulled forward. There’s a true street wall there,” says Sellars. “You don’t have that in Chicago very often.”
A three storey brick house, sitting right next to the sidewalk, right next to its neighbors. If anything, these challenges reminded Sellars more of South London than Chicago. The facade could have easily imposed over the street below. Sellars needed to break down the scale of the building. His first tactic was to visually knock back the corners of the building.
“If you’re worried about a facade being so massive, knocking the corners back does a lot,” Sellars says. “It keeps it from being a hard line to a little more fuzzy line.”
To do this, he took advantage of the custom bricks Bricks Inc. sourced from Vermont Brick. Scores of hand-molded bricks form a scooped column at the corners of the facade and make Sellar’s fuzzy line a reality.
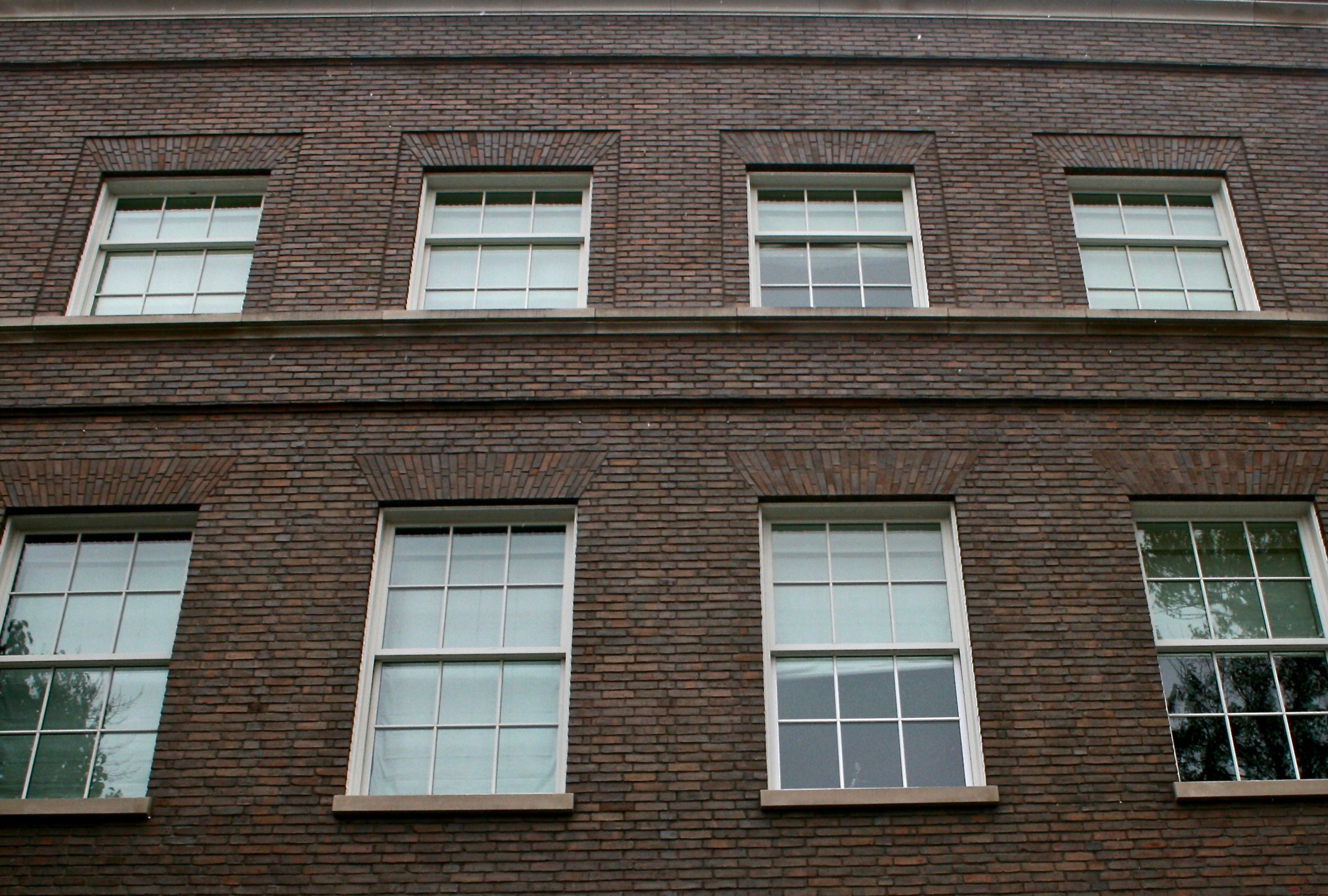
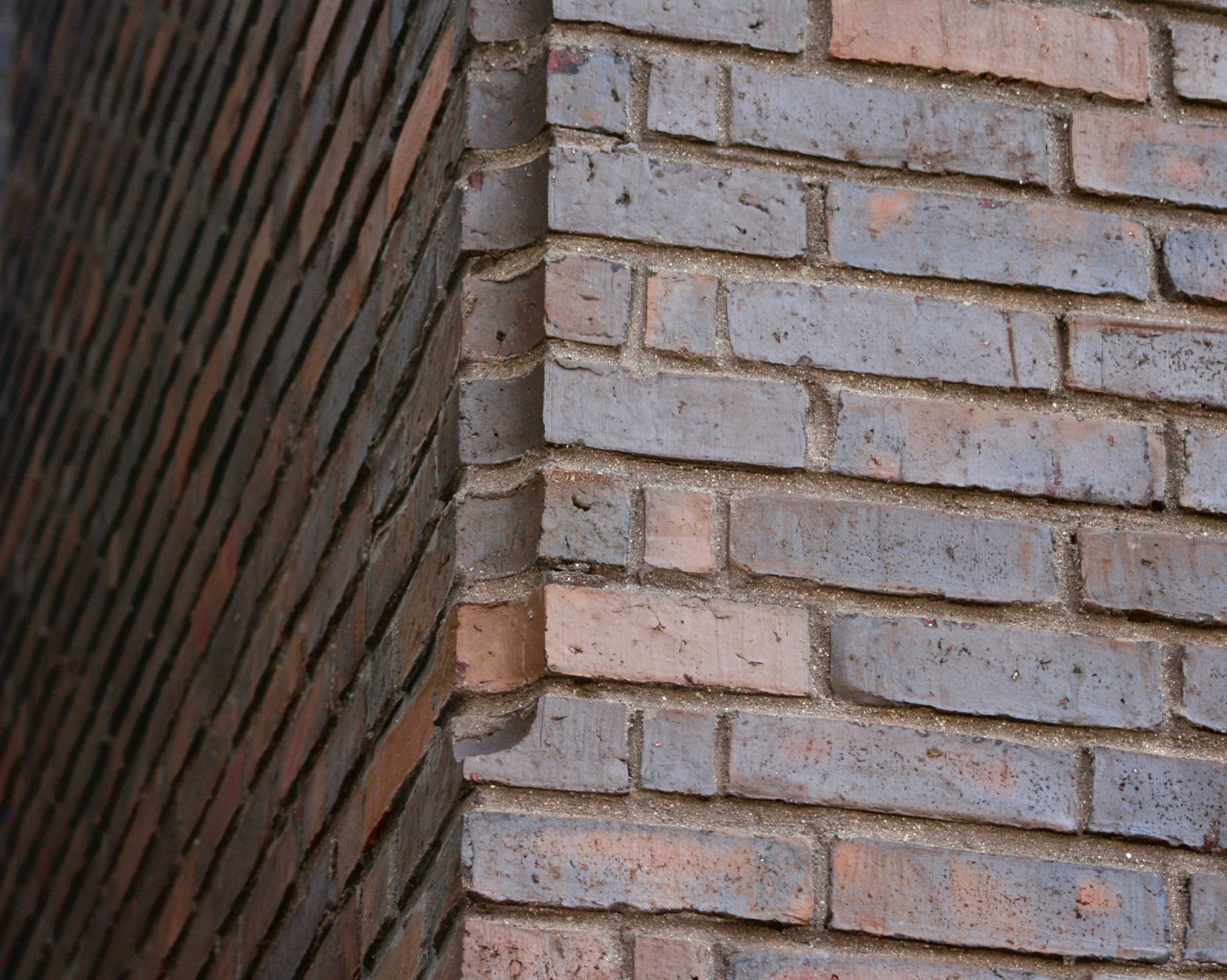
The next step in reducing the scale of the house was to reduce the perception of the vertical mass. Sellars designed the house as a “two storey volume, with a smaller one on top.” The top storey is divided from the rest by a sort of false cornice: scooped bricks flare out into several courses of stretchers topped with a limestone band, upon which rests the third storey.
Custom bricks also helped achieve a subtle visual separation of the storeys as well. The first two storeys feature ½ bricks in every other course, which trace faint vertical lines over the facade. The bricks in the third storey are laid in simple running bond, giving emphasis to the horizontal line, in contrast to the bottom storeys’ subtle vertical.
Between the ½ bricks, scooped bricks, and even small ⅓ bricks (used around the windows as a nod to brick firestops used in the Georgian townhomes of South London), Bricks Inc. sourced over 20 custom hand-molded shapes for 1853 N Burling.
“Specific molds were made for each and every single one of them,” says Brent Schmitt of Bricks Inc. “It was like a giant jigsaw puzzle.”
Nowhere on the house was the power of this statement more true than on the arched doorway.
The Door
For the door to the house, Sellars once again took inspiration from Georgian architecture. “When you look at houses in South London, things are very close to the street,” says Sellars. “So the openings matter tremendously.”
The door to the house was designed to scoop inward, an invitation amidst the wall of brick. The question then became how to achieve this scooped arch.
For Sellars, there was a simple way and a right way.
“There was a lot of debate. At some point, someone suggested a keystone,” Sellars says. A keystone at the center of the arch would have allowed for more flexibility, more wiggle room in laying brick. It would have not required perfectly shaped bricks. But it would have been wrong.
“This thing needs to fold and wave in,” says Sellars. “[A keystone] would have removed that emphasis.” The simple way was out. To Sellars, the arch needed to be entirely of brick.
Brent Schmitt of Bricks Inc. calls it “a 3D arch.” It’s a fitting name. Each brick in the arch is perfectly shaped in three dimensions to perfectly fit in its place. As the bricks on the front edge taper from top to bottom, they must also taper backwards to fit into the scoop below the arch.
An arch made of perfectly fitted, intricately shaped bricks required a special manufacturing process. The tightness of the fit meant that individually molded bricks would be too variable. So if you can’t make your arch with a keystone, and even carefully shaped bricks are too variable, how do you make Sellars’ folding and waving arch?
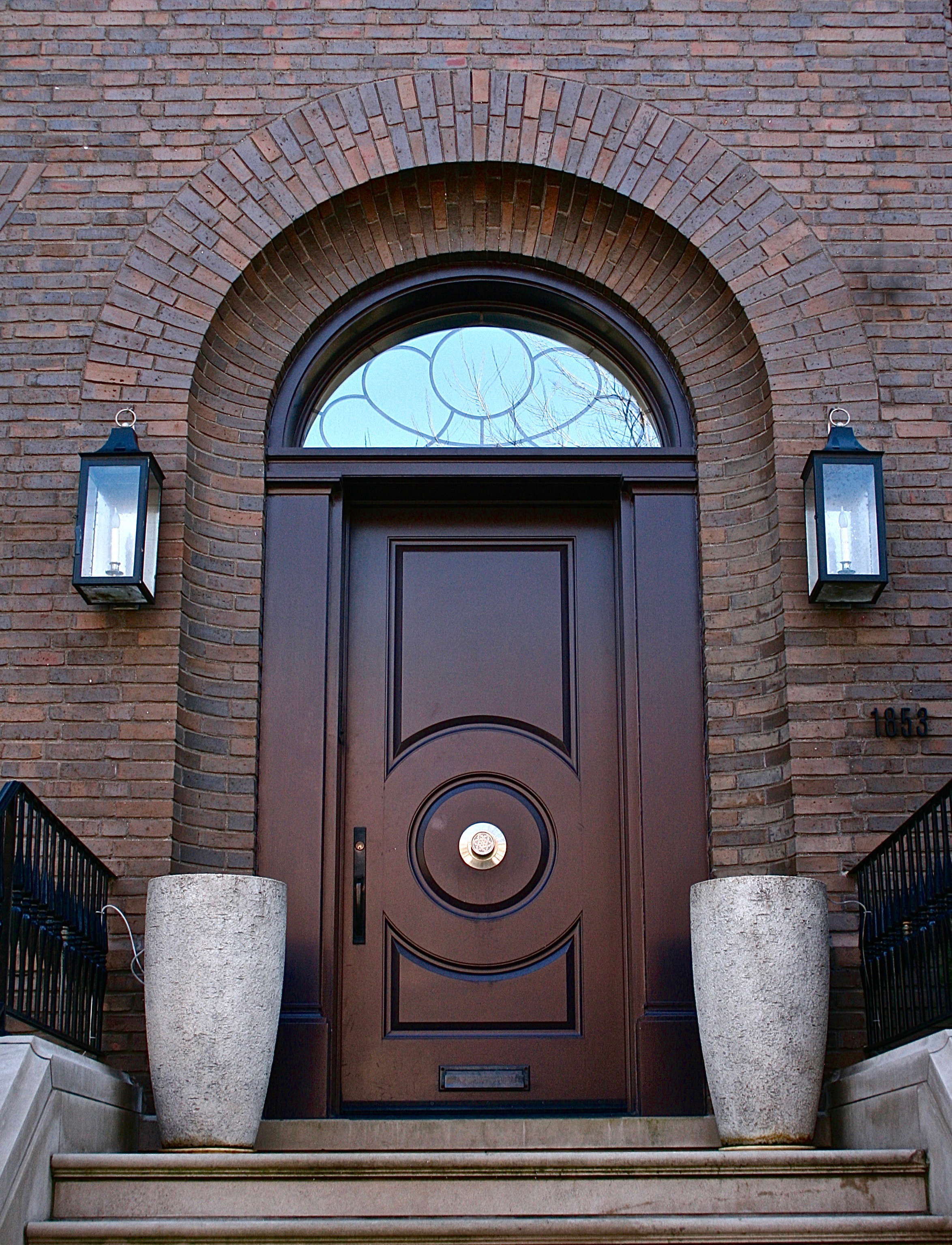
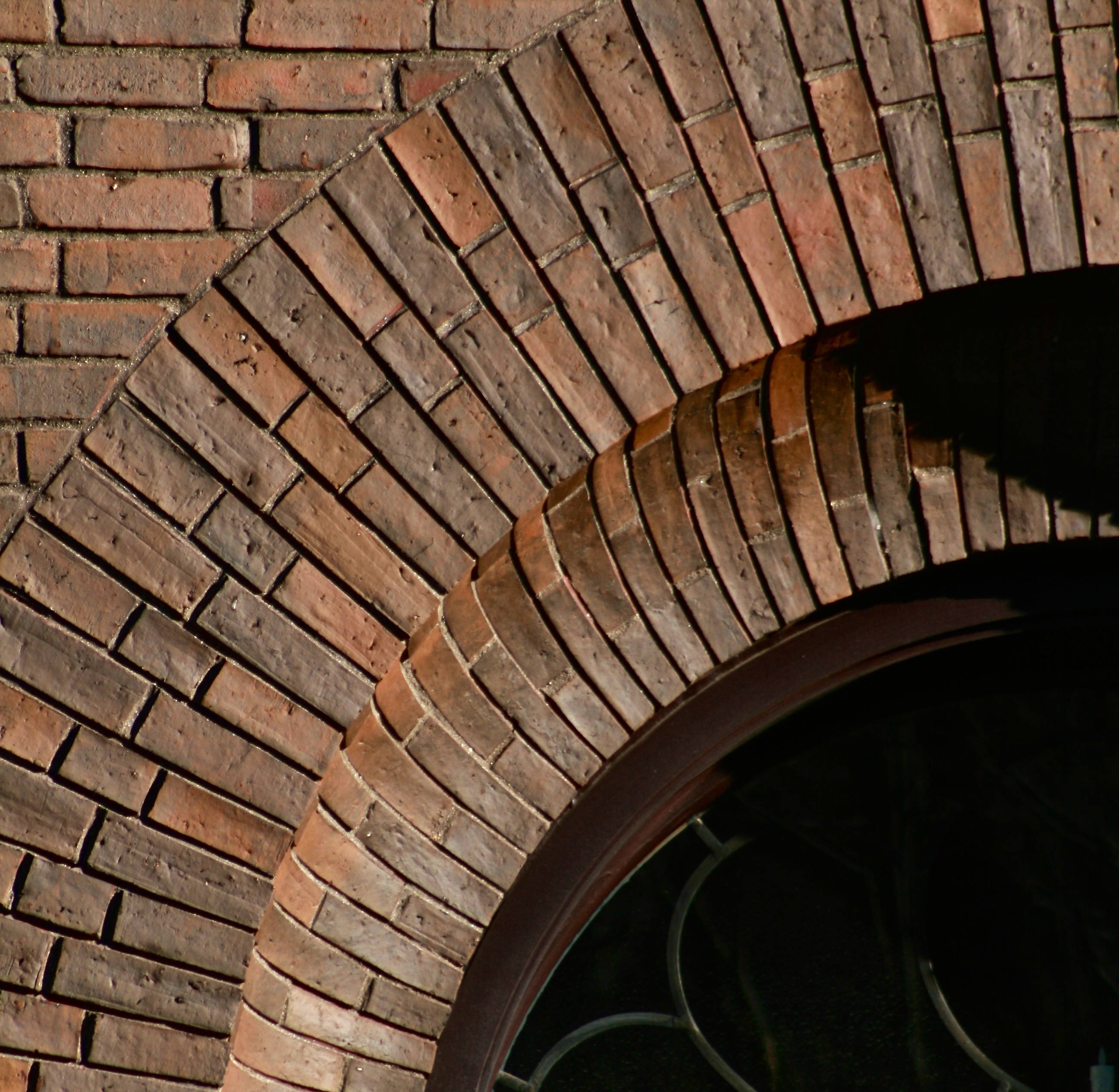
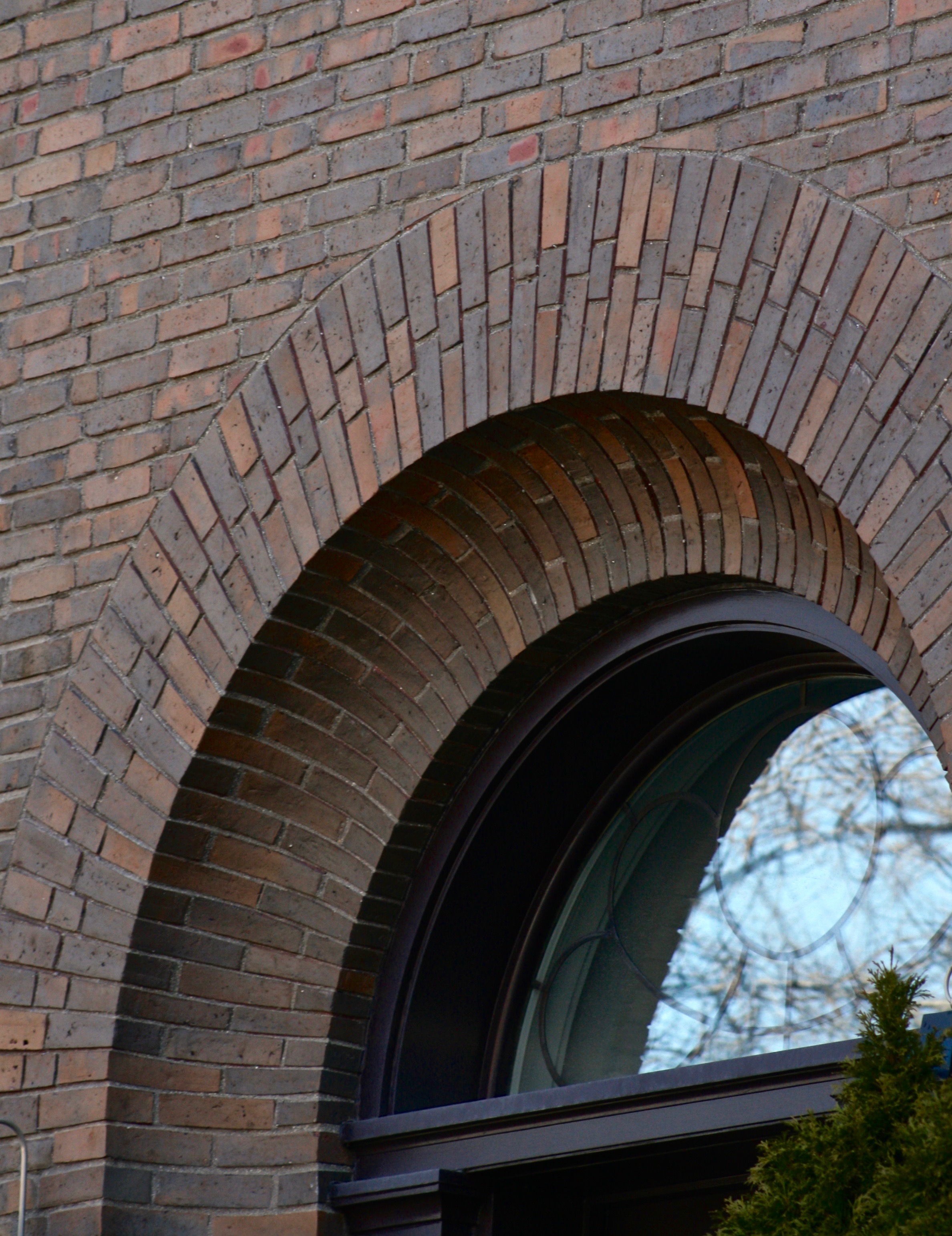
You make the whole arch all at once.
Vermont Brick molded a massive slug of clay in the exact shape, size, and dimensions of the arch. The slug was then fired along with all the bricks to keep a the coloring consistent across the house.
Once the slug was fired, the individual bricks needed to be cut from the block. To establish the necessary cuts the contractor on site and the brickmakers needed to be in constant conversation. “You had to have section, plan, and elevation drawings of the arch,” says Schmitt. “They make a one inch to one inch template that comes out, they establish ‘yes this fits’ and sign it and send it back.”
“You’re UPSing huge documents back and forth to just ensure that it works perfectly,” Schmitt adds.
Vermont took these exacting drawings, laid them against the slug and cut out each three-dimensionally tapered brick. In the cutting process, they not only needed to account for the thickness of the mortar that would be laid in between each brick, but also of the thickness the blade itself.
The process was painstaking, to be sure. But the results are remarkable. As Sellars puts it, “that is what gives [the house] its life as you’re walking down the street.”
With the design complete, the brick fired, and the arch cut, the Bricks Inc staff worked closely with Vermont Brick and the masonry subcontractors at 1853 N Burling Ave to keep everything running smoothly. For Schmitt, that required planning, scheduling, and foresight. Most notably on this project, that meant firing extra slugs of the arch. You’re gonna break a piece, and with a slug already ready, a replacement brick was ready in no time.
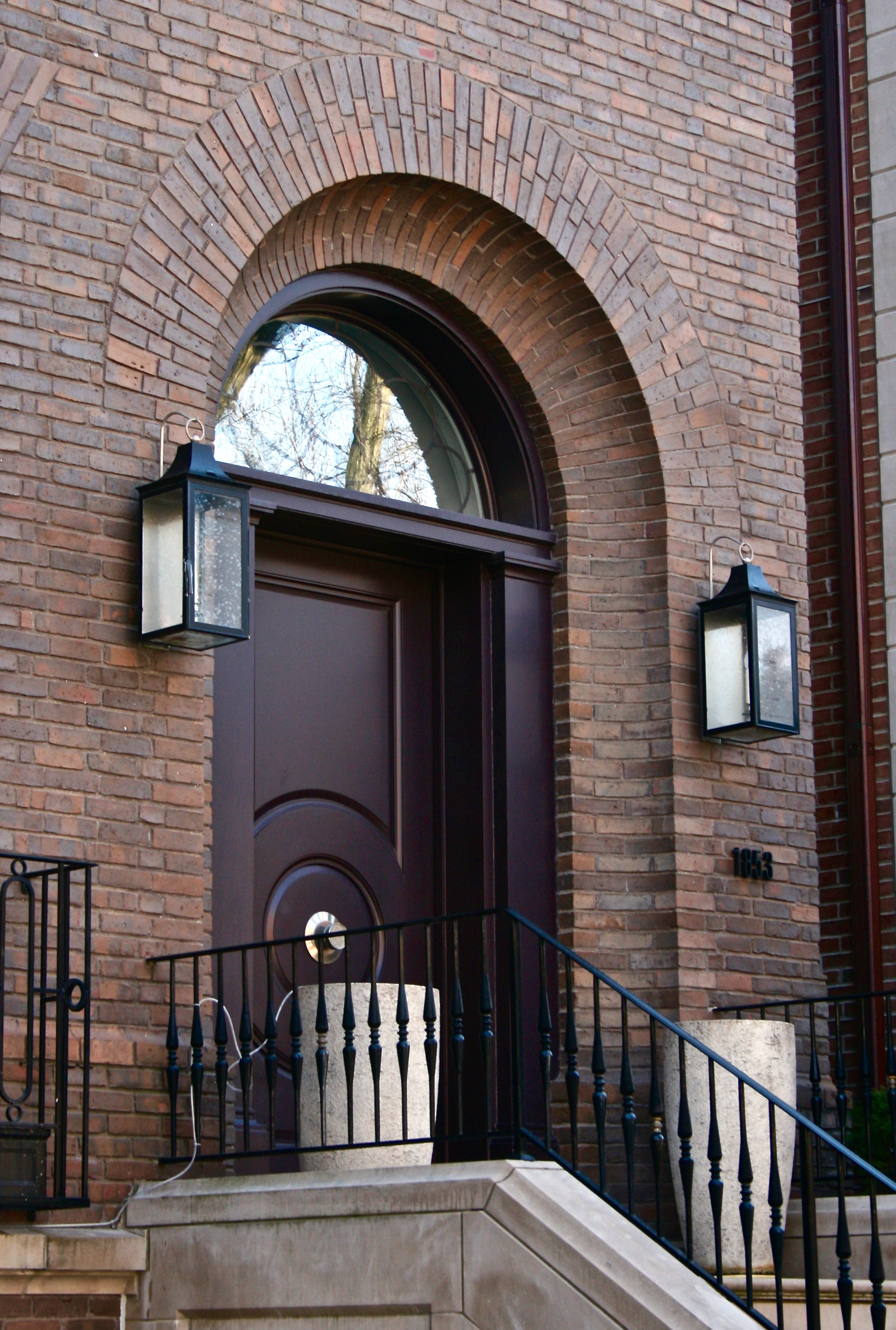
The Bentley Hoffmeister Home began with a picture of a brick wall. From there, Brent Schmitt and Bricks Incorporated found the homeowners a waterstruck brick that matched their vision. He worked with the manufacturer to match brick to their aesthetic, and he found architect Robert Sellars over 20 custom bricks to make the house stand out from the street.
With Bricks Incorporated, a brick wall can become a Georgian-inspired home of intricate and bespoke brick.